10-03-2021
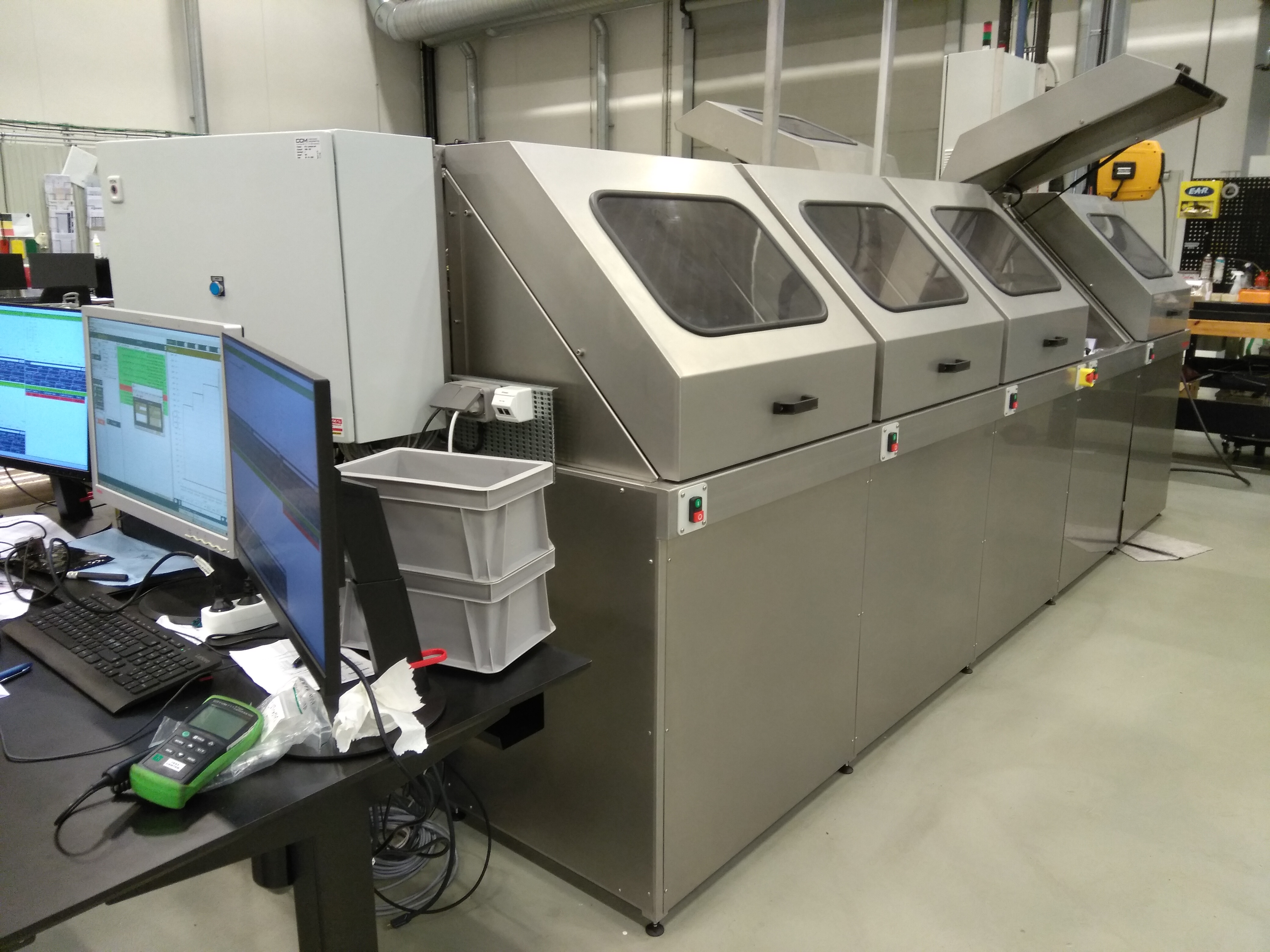
Valve Test Station at Welltec
Welltec produces material for downhole pumping, such as oil production or in geothermal powerplants. This requires pipes that can withstand very high pressure of thousands PSI, and in them valves controlling the flow - there is no room for error. This is an automation case study of a test station for these valves.
Valves in downhole production allow for connecting reservoirs underground but can be also used for simple one reservoir mining. As you can imagine, the pressures of oil or steam underground are very high. The pressure changes across the pipe but also with time, as a reservoir is emptied out. The direction of flow inside the WAB (Welltec Annular Barrier) switches as the pressure reaches certain threshold, after the pipe has been deployed and before it is used for production. This happens thanks to a pin which breaks at the given pressure.
This process is irreversible if the valve and pin are inaccessible deep underground. There is no second chance and everything must work out perfectly on the first try. Each solution has a unique valve configuration, consisting of different number of valves operating in different temperature and pressure conditions, shearing at different pressure points. These factors affect the material friction of the valve. This means that every valve is tested for its purpose application, several times. In fact, each valve would go through approximately 5 tests, at least 3 tests to confirm the right pin size (or more, if the right type was not the first try), and 2 leakage tests.
The tests were done manually, each taking around 45 minutes. That means that a testing of a single product took around 4 hours! In addition, as 4-5 people were doing the testing, there could have been a minor variation in how the test is performed. The goal of the project was to remove this bottleneck and ramp up testing to 20 valves during an 8-hour shift, performed by one person. Thus, it was decided to automate the process, consequentially also increasing the repeatability of the process. Simple mathematics results in a test station with 10 separate testers, which can test up to 10 valves at the same time.
The station and valve fixtures themselves were developed by Welltec, as they need to fit to different valve types, whose design is a trade secret. “We need to be absolutely sure that the tester works correctly and can identify any errors,” says Claus, manufacturing engineer and production equipment project manager at Welltec. “There is no use having a machine if the worker would need to re-check everything, it would not be possible to keep an overview of 10 tests. Easy-to-use interface and a clear overview were very important, for example green and red color to distinguish un-successful tests.” This is where CCM – Electronic Engineering comes to help.
Each fixture has several sensors, monitoring the shearing conditions, especially the shear stress. The pressure ranges from 0 to 20.000 PSI (that is 137,9 MPa), so the sensors need to be very durable to operate accurately after many cycles. The data is then processed and visualized using LabVIEW software, which is our specialty. The operator has all the needed information on 3 screens, where data is intuitively arranged and clearly indicates which tests were successful using a color scheme, just as requested. The test status will be also visible on large screens above the setup. Using the controlling panel, the operator also calibrates the equipment and controls the test conditions, which ensures repeatability of the tests. The valve fixtures are exchangeable, which means that the test station with different set ups can be used for any type of valves Welltec produces.
According to Claus, the biggest challenge was formulating the indicators which the software uses to identify errors. The valve manufacturer cannot risk neglecting a quality issue and delivering faulty products to its customer. Normally, the evaluation is done by experienced operators, so we had to “teach” the program how to perform the task. Robin, one of our software engineers, agrees that a lot of the effort was used on translating the project requirements into programming tasks.
As a part of the Valve Test Station site acceptance test, all valves will afterwards be also tested manually to be 100% sure the solution works flawlessly. However, once the Test Station is in full use, it will be a huge productivity improvement. “The investment will return almost instantly” by removing a bottle neck and augmenting workers to perform quality inspection 10-times faster, says Claus.